Sheet metal bending is one of the most common operations. You can call it as folding, braking, flanging, die bending, and edging.
Sheet metal bending is when a single flat piece of metal is deformed through force. This force must be applied evenly across the workpiece to achieve a bend. The final result is a permanent change in the shape of the piece. Metal bracelets are just one example of what can be achieved with a simple sheet metal bending process.
But do you know? What are the most common bending methods? How to calculate bend allowance?
We will discuss all these questions in this blog and some bending tips. We would unfold every aspect of sheet metal bending.
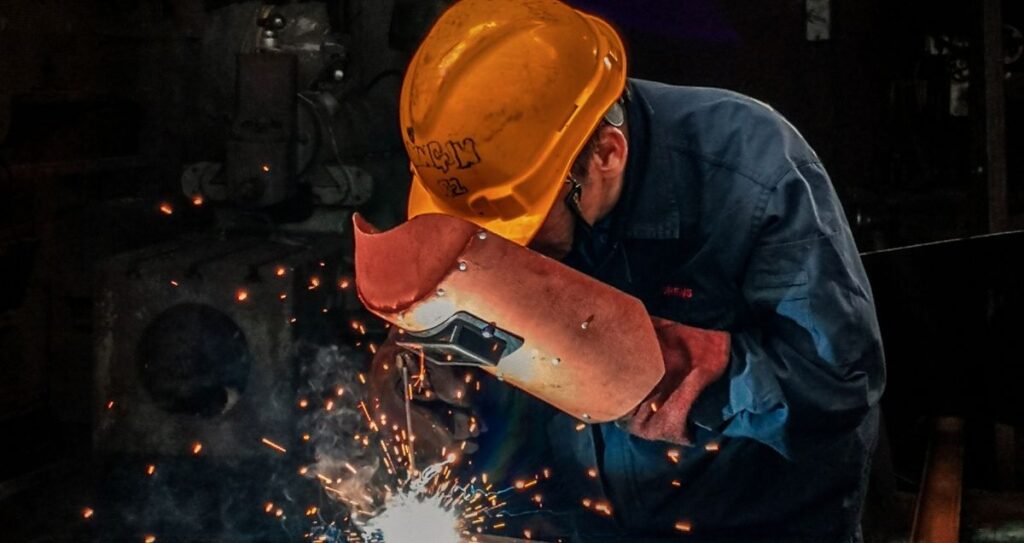
Sheet Metal Bending Methods
Whether you have your own company that does lots of bending, or you’re a hobbyist who does it just for fun, you should always be looking for ways to improve the overall quality of your bending projects. It might not have occurred to you before, but there are multiple methods for bending sheet metal. And Each has its advantages. The problem is usually between accuracy or simplicity, while the latter gets more usage.
V-bending method
The V-Bending method is the most common sheet metal bending method. This is because it is the most accessible workable sheet metal that can be usually completed in 2 or 3 steps. In this method, an instrument is a punch, and v-die gets bend sheet metals to a required angle. The bending punch presses on the sheet metal placed over the V-die. After that, The angle formed by the sheet metal depends upon the pressure point of the punch.
V-bending is used for most bending projects. Bending stock material to fit a contour of a pre-existing component is what a v-bend does. This method you can use in automotive fenders, grills, vans, trucks, and RVs.
The V-bending method can be classified into three:
- Bottoming
- Coining
- Air Bending
Roll Bending Process
To bend sheet metals into rolls or curved shapes, you can use roll bending. The method employs a hydraulic press, a press brake, and three rollers to make different bends or a big round bend. This process forms cones, tubes, and hollow shapes.
U-Bending Process
The U-bending process is similar to the V-bending process. It uses the same instrument and method. The only difference is that the result in terms of the shape is U-shaped. U-bending is very famous. Moreover, other methods produce the form flexibly.
Wipe Bending Process
Wipe bending is a sheet metal working process used to create almost flawless bends. It is free of the double scarring found in taper dies. Wipe bending allows the metal shape using just one piece of metal. The wiping dies is possible. It enables the metal to shape and when in operation.
Rotary Bending Process
In the process of bending, scratching is produced by the tool. The rotary Bending Process does not lead to scratching the material’s surface. It is also ideal because it can bend materials into sharp corners. Therefore, it has become a must-know skill in sheet metal work workshops.
Sheet Metal Bending Allowance
So, what is bend allowance? Bend allowance is a manufacturing term that refers to the allocation given to accommodate sheet metal’s stretch and bending.
When sheet metal is bent from its original flat shape, its physical dimensions will change. The force employed to bend the material causes the material to compress and stretch on the inside and outside.
This deformation changes the sheet metal due to the exerted force of compression and stretching on the bend. The length calculated from the bend’s thickness between the inner surface and the exterior remains the same. And we called this a “neutral axis.”
Bend allowance examines the thickness of the bending angle, the method employed, and the K-factor. Bend allowance measures the compression ratio on the inside line of a bend to the tension on the outside of the bend.
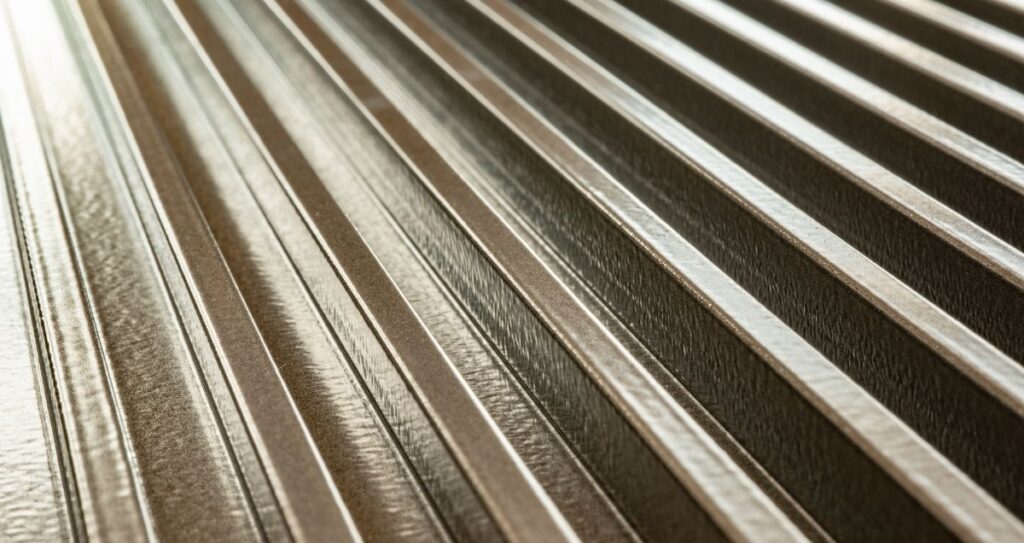
Questions you may ask before bending a sheet metal
What is the best sheet metal bending method?
All sheet metal bending modes serves various purposes and produces multiple shapes. So, the best bending method depends on the material’s goal as per shape.
Is sheet metal easy to bend?
Bending steel plates is not that easy. But, with an understanding of the process, it can become manageable. Firstly, you need to understand the methods to use and the tools available. You can go over the article to get familiar with the process.
Conclusion
So that wraps up our discussion of different methods for bending sheet metal. Remember, though, that the correct solution to your particular problem will depend on the type of material you are using and the shape and size of your finished piece. If you have specific questions about these topics, don’t hesitate to contact us or another professional in your area!