Delahenty Machinery, a trusted name in Australian manufacturing, has become a key player in designing, producing, and supplying high-quality bending tooling solutions for a variety of industries. With decades of experience, the company specialises in producing precision tooling components for tube bending and end forming applications.
Need a tool set built quickly? Our engineers and design team are ready to help.
So, why wait? Call (03) 9800-1544 and take your tube bending processes to new heights of precision.
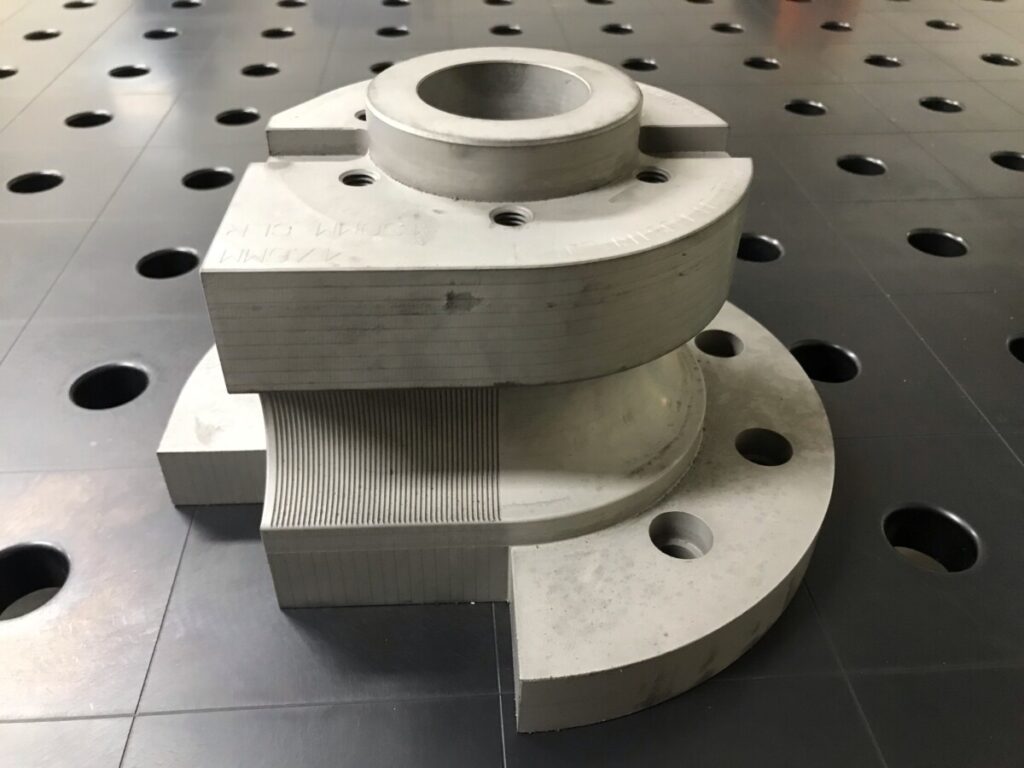
High-Quality Tooling Solutions
At the core of every forming application, tooling plays a vital role, and Delahenty Machinery has dedicated itself to providing only the best. The company designs and manufactures complete tube bending and end forming tool sets, ensuring customers receive top-notch tools and rapid turnaround times. Their product offerings include:
Bend Tooling
End Form Tooling
Mandrel Links and Balls
One piece and Tip Type Wiper Die
Ball & Plug Mandrels
Advanced Mandrel Options
Delahenty Machinery offers an extensive selection of mandrels for various applications, made from both tool steel and aluminium bronze. Some of the available types include:
Close Pitch Mandrels for thin-wall and tight-radius bends
Chain Style Mandrels
Plug and Spoon Mandrels
Square, Rectangle, and Oval Mandrels
Plastic, Tool Steel, and Aluminium Bronze Mandrels
Mandrels for Extrusion Bending
Custom Body Lengths and Thread Options
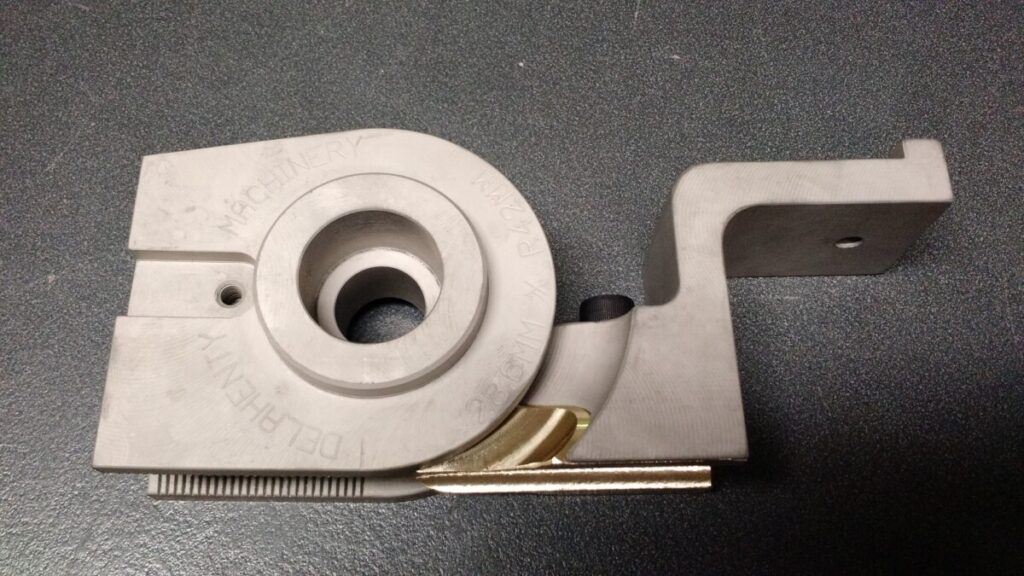
Wiper Dies and Re-Cut Services
The company also manufactures a wide range of solid wiper dies, including both tool steel and aluminium bronze variants, with mounting options suitable for all manufacturers. Their re-cut service offers fast turnaround times for:
Solid wiper dies
Tip type wiper dies
Re-boring and re-cutting of wiper dies
Comprehensive Tooling Sets
Delahenty Machinery excels in designing and manufacturing complete bending tooling sets, tailored to customer needs. These include:
Full Bend Tooling Sets
Interlock Tooling
Square, Rectangle, and Oval Tooling
Extrusion Tooling
Empty Bend Tooling
Controlled Wrinkle Tooling
Split Tooling Designs
Collets
Twin Head and Press Bend Tooling
Solid and Flat Bar Tooling
Quick Change Tooling Designs
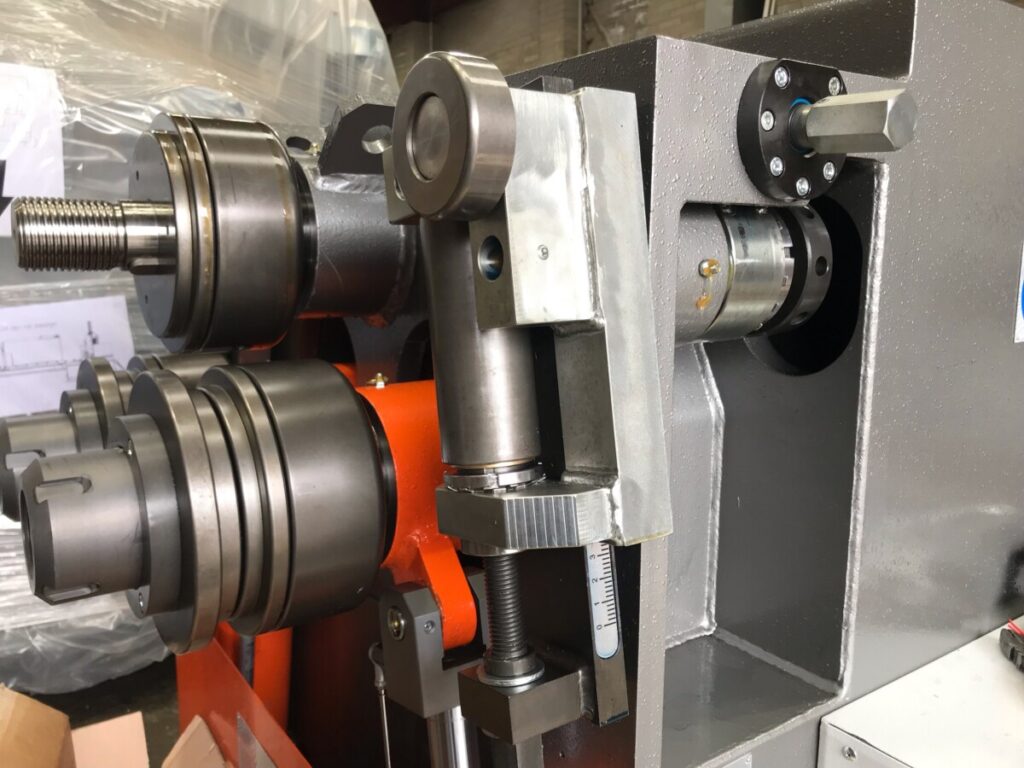
Section Roll Tooling
Delahenty Machinery also offers specialised roller solutions for profile roll forming, available in both steel and nylon. These rollers are designed and hardened to handle materials such as steel, aluminium, and stainless steel.
Expert Tooling Design & Development
All tooling is designed in-house in Australia using 3D CAD software, ensuring precise and efficient production. Delahenty Machinery is committed to meeting both production and budget requirements, offering a range of design services, such as:
- 3D CAD Tooling Design
- Tooling Prints and Quick Replacement Manufacturing
- Ongoing Tool R&D and Bent Part Simulation
- Tool Steel Selection and Price Estimation
- Reverse Engineering of Tooling
With an unwavering focus on quality, innovation, and customer satisfaction, Delahenty Machinery remains a leader in the Australian tooling industry, offering customised solutions for even the most complex forming and bending applications
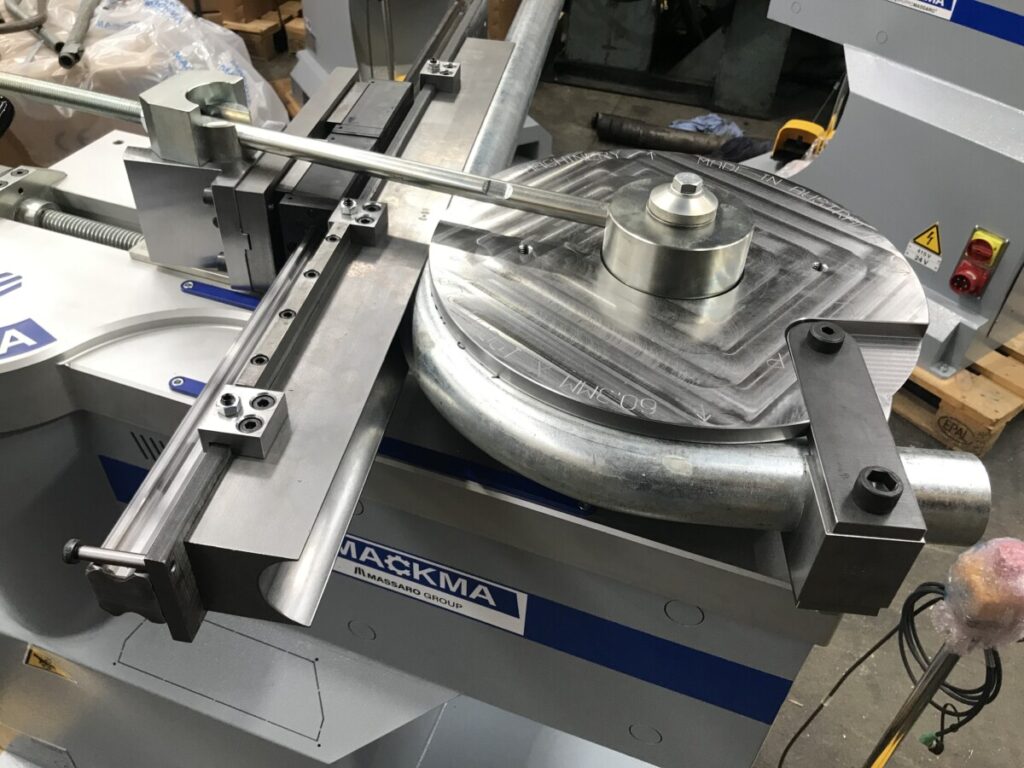